Have you felt it yet?
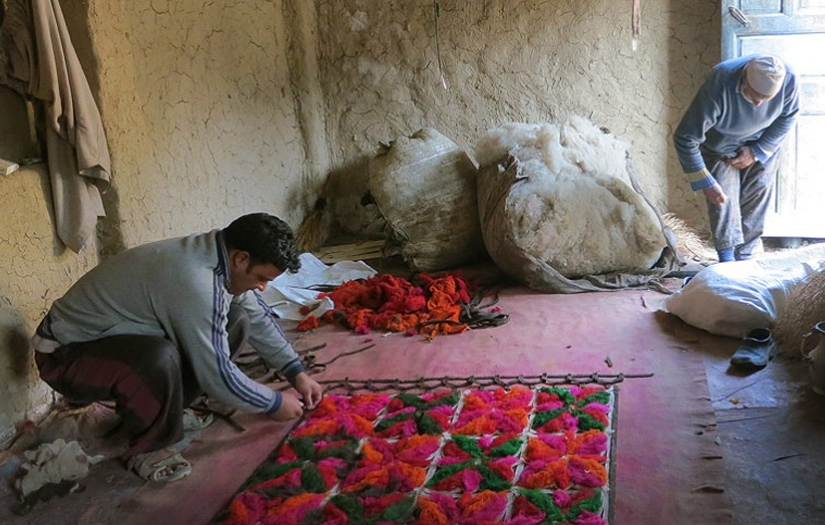
It’s as if the fully matured leaves of the Chinar tree are in perfect synchrony with nature’s music of the fall; as they gracefully part from their mother twigs and ballet their way down to merge into the ocean of golden-red autumn-struck leaf kind. Through centuries spell bound poets have lost themselves to romance with the valley, but even a momentary gaze at the beauty of this red carpet laid by nature to welcome the sublimity starved outsider, is enough to have masses indulge in poetry.
And as if these carpets reveling nature’s opulence weren’t enough, there are the other kind welcoming the outsiders to quietly let themselves get lost in this paradise on earth. At srinagar Namda is the craft of making carpets by felting. This craft is said to have traveled to Kashmir from Iran along with a Sufi Saint, ‘Amir kabi Shah- e-hamdan’ many centuries ago (600yrs to 700yrs). Accompanied by master craftsmen who excelled in woodcarving, weaving, namdakaari, woven carpets, Papier Mache et al, the saint came with a noble mission to generate work opportunity for the locals. This noble endeavor of the saint is a living heritage that continues to be one of the prime occupations and source of livelihood for the people of the valley even to this day.
The pedigree of 49-year-old Fahrooq Ahmed Khan has preserved the spark of this skill through generations now. With his grandfather, father and 33 years of his own life dedicated to the pursuit of keeping this flame alive, the art of felt making has almost become genetic. But Fahrooq ji refuses to train his successors, forhe believes that this one craft seeks a whole lot of physical strength and remunerations are hardly comparable. His 13 member team is now reduced to a one man army. Such unanimous sentiment amongst the craftsmen community is the reason that the number of craftsmen involved in this craft has dwindled from 400-500 to a mere 100 over a span of 15 years.
The felted carpets are predominately made of pure sheep wool. Cotton may also be added in varying ratios (70: 30) to increase the thickness and whiteness of the end product. However, pure wool carpets are much warmer.
The sheep wool ‘kat yer’ required for this technique is locally bought from Badgam, Pahalgam (inhabited by shepherds) and Naushera (where the Govt. House for wool distribution is stationed). Namdas made from Kullu kangada wool are known to have more strength. ‘Marino’ is another quality of fine wool, imported from Australia in modern days. Carding is the process by which impurities settled within the wool are removed and a uniform & consistent thickness is achieved.
Earlier the process was carried out using hand operated wooden tool called as ‘dhooin’ in the local language. Primarily a bowstring and stub kind of arrangement that allowed the fibers to disperse into thin flakes, as the stub is struck against the string near the heap of sheared wool. The wooden system is suspended from ceiling on a curved bamboo section to allow carding. Today however most of the necessary carding is carried out in mills. Bimla woolen mill, a government initiative to facilitate the craftsmen with carded wool was established in Srinagar city 40 years ago. Besides these, two mills have been established in Gandarbal as well.
traditional geometric patterns if the base is colorful) is marked upon the jute base with a charcoal. Woolen flakes are evenly spread all over it. It’s a trick of a long curved stick in one hand and the carded wool in another and how the craftsman juggles with it to form a cloud of wool with even density. The skill is used to place and relocate the wool over the marked lines on the base mat.
Namda is usually a sandwich of many (minimum 3) such layers flattened over each other. The order of placing the individual layers is such that the design is laid upside down, which means the topmost layer is laid first. Hence, all the collected wool is divided into three piles. This division is usually based on 1. The color/patterns you want to show on top 2.There are always surplus remains of wool left from each Namda that has been recently made, all such wool is combined and put as the lowest most layer (not to be seen but pure wool makes it durable and warmer).
After a layer is spread, it is sprinkled homogeneously with water and pressed with a tool known as ‘pinjra’ (woven willow wicker). For a carpet that is 2kg in weight, 2 liters of water may be required. In winters warm water is used. Consequently the intermediate woolen layer is laid and pressed into uniformity. The ultimate layer is eventually placed, wetted and beaten till consistent.
The sandwich of wet wool is then rolled tightly from one end with the jute mat and the anchor metal rod. Muscular pressure has to be applied over a period to keep rolling it tighter and squeeze the water out. The process of rolling and pressing is carried out from 1 to 3 hours depending on the quality of wool used (local wool is coarser and felts faster) and also on the ratio of cotton used (more the cotton greater the time). The craftsmen use their feet to apply pressure on the carpet. The role is eventually opened and checked for inter-layer cohesion, lumps and evenness.A special soap with increased caustic content is then poured over the Namda. It is rolled once again with hands and without the mat. The carpet so obtained is known as a ‘kachcha namda’, the strength of which is further increased by binding the edges.
A dry wash is usually carried out by the women folk on the nearby ghats after 1 to 1.5 hours to remove all the soil content from the carpet. Hand embroidery ‘Aari Kaam’ using colorful dyed threads and the ‘aari’ needle is carried out if the Namda is a traditional one. There are also examples of some beautifully crafted carpets by stitching the pieces of old worn out Namdas together, with appliqué technique.
Since this work requires great muscular strength, it is usually carried out in winters.The craftsmen move to relatively cooler places like Kargil during summers. These Namdas are generally sold through stalls at ‘Craft Bazaars’. Although the craftsmen have no overseas exposure, local bodies set up to uplift the state of the craft sector in Kashmir, hold regular workshops to contemporize the nature of the designs and patterns so that it may become marketable to a larger section of consumers.
In a land that has seen chaos and ever failing systems over two decades now, beauty still finds a way to seep through. Through crafts like Namda, one must appreciate the endeavoring spirit of the Kashmir craftsman who has managed to preserve the precarious honor of the craft, while standing on the edge himself.
Paula
Hello there, I just bought a beautiful and colorful Kashmir Namdha from a flea market, I’m so happy. I had never heard of the word Namdha before but thanks to a little informative fabric label on its reverse and to your post now I know what a wonderful thing I own. Some of the embrodery is damaged (I can try to fix that) but what concerns me most is that the rug is stained (yellow stains) so I wonder if you know how I can clean it. I read somewhere that dry cleaning could damage the rug 🙁
Thanks in advance!!
Paula.
Tushar Upadhyay
Wow beautiful design. These carpets is looking so different. Well done craftsmen
Jane Courtland
Could you give me an estimate on an old kashmir embroidered felt rug? I could send a photo to you,
Thank you-
bellearorb
Hi :). I am from Netherlands and i don’t know how can i disable my signature? Regards 🙂
SandraJam
I’m not just inviting you! But it will be interesting for sure loveawake.ru