Threads of Heritage ~ Indian Silk
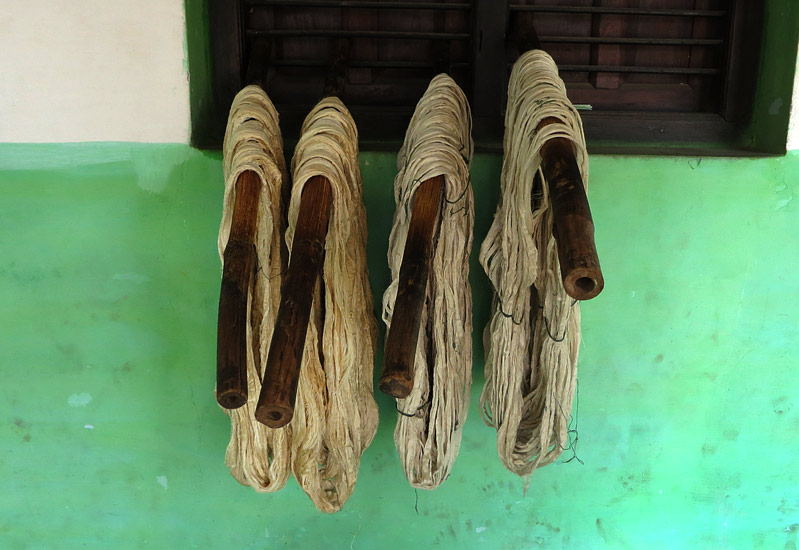
Recently, Balkrishna Ravi’s son, Sudhir, had taken a newfound interest in sericulture, the livelihood for around a million people just in their state, and Ravi decided to take him on a mini field trip to the pride of their village, the cocoon market at Sidlaghatta (raw material market for indian silk). Although quite overwhelming for a young boy, Ravi believed that the first stop on their trip would give Sudhir an eye-opening experience of the largest cocoon market in the country. The father-son duo eagerly observed the chaos of people placing their bids to get the best quality cocoons at exorbitant prices.
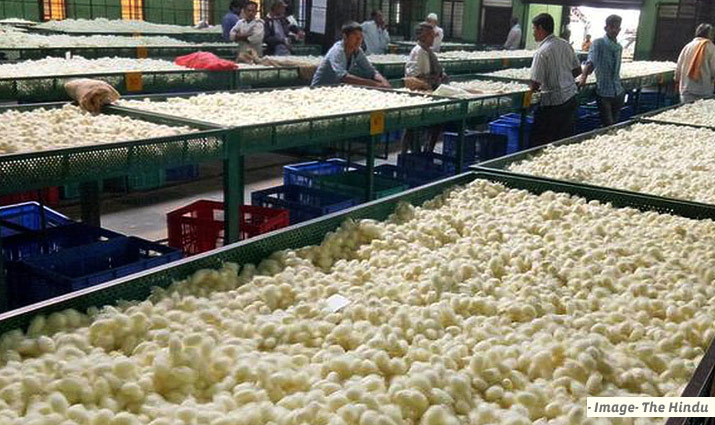
The next stop on the trip was the small and cramped rooms for silk reeling, the gruesome end of silkworms, and the beautiful beginning of silk making. Surrounded by the dingy smoke and steam in the near-dark rooms, Sudhir watched as the cocoons were dunked in boiling water to unravel them without breaking the silk fiber. Beautiful silk fibers were obtained at the cost of hundreds of silkworm larvae. Sudhir was curious to learn more about the silk and the silkworms that helped create the cloth of his mom’s most exquisite sarees. He was particularly fascinated by the Bombyx mori, which makes the well-known mulberry silk, and is completely domesticated and reared indoors; its name derived from its interesting diet of the leaves of mulberry plants. A significant part of Sudhir’s fascination lay in the fact that mulberry silk contributes to around 79% of the country’s silk production. This was quite mind-blowing to a young boy who had only ever known the local process of silk-making, even more so to learn that states other than Karnataka, such as Andhra Pradesh, West Bengal, Tamil Nadu, and Jammu & Kashmir contribute to the familiar raw mulberry silk.
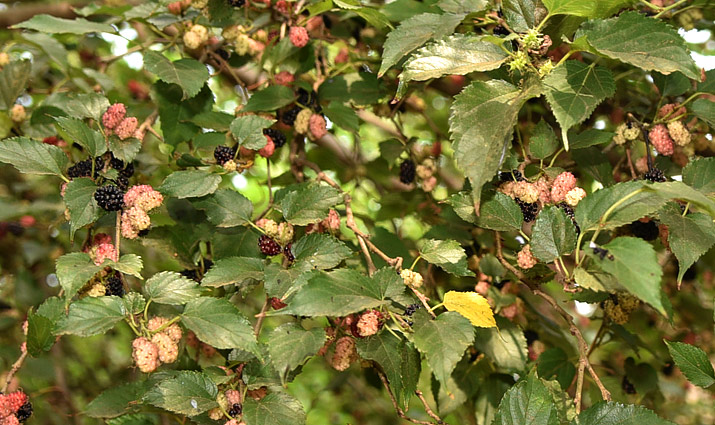
Sudhir had a knack for noticing minute details and an urge to curb his curiosity about them, which Balkrishna had no qualms against obliging to. Balkrishna was equally passionate about sericulture and was eager to impart his knowledge of different silks to his son.
While mulberry silk is a relatively popular silk variety, the Vanya (non-mulberry) silk has a charm of its own. The tropical tussar from the silkworm, Antheraea Mylitta, and the temperate tussar from the Antheraea Proylei thrive on food plants such as Asan, Arjun, and Oak. Compared to mulberry, these silk varieties are reared in natural conditions on their trees, particularly in Jharkhand, Chhattisgarh, Orissa, Maharashtra, West Bengal, and Andhra Pradesh. Tussar culture has been the mainstay in many tribal communities of India, another reason why Bangalore dwelling Sudhir did not know much about these silks. While mulberry silk, with its yellow, white, or greenish-yellow color, is known for its shininess and softness, factors that make it the ideal silk to produce intricately designed and opulent robes, the tussar silks are a copperish color that lacks a specific luster and is mainly used for furnishings and interiors.
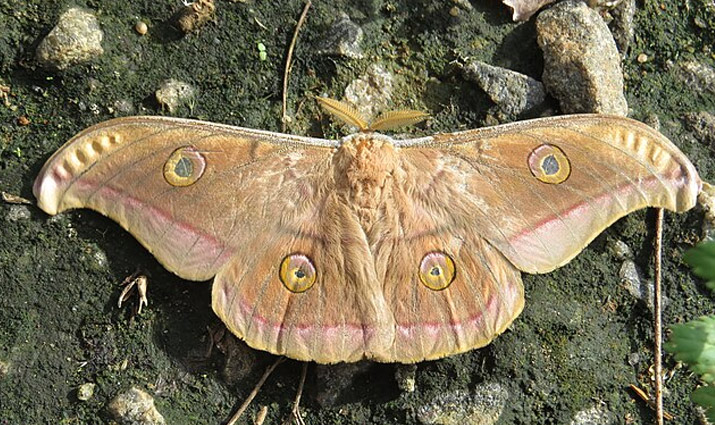
Far from the familiarity of Bangalore, Sudhir was next introduced to the Golden Treasure of Assam, muga silk. Made from the cocoons of semi-domesticated silkworms belonging to the Saturniidae family, Antheraea Assamensis, that thrive on Som and Soalu leaves, and mainly produced by the Garo community, the muga silk holds the title for one of the strongest natural fibers. With its extreme durability and natural glossy yellowish-golden tint, this silk was reserved for royalty and often compared to being as expensive as buying gold, a fact that left the little boy in complete awe. This fabric’s one-of-a-kind shine tends to improve after each wash, which means that the product can possibly last a lifetime, making it one of the costliest silks. The popularity of this silk has only grown over the years, especially with its apparent monopoly in Assam, now considered a coveted item for traditional wear for extravagant occasions. A sought-after local fashion item from the muga silk, the Muga Mekhela Chador is a traditional dress of Assamese women. Classic motifs on the fabric such as Jappi (the typical Assami topi), Miri Gos Butta (a pattern of miniature tree motifs), and kabutar (pigeons) and pure jari work give the fabric an extremely royal and classy feel, amping its desirability as well.
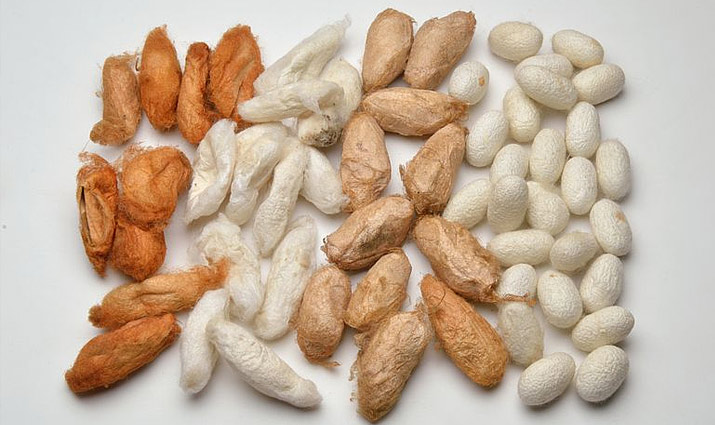
With further curiosity, Sudhir inquired of his father about the time since they have been taking help from that small bug to prepare their clothing. Balakrishna laughed and said, “I don’t know since when, but you know when scientists observe a bangle found in the Harappa site, they discovered silk fiber in it. So, we can assume that women were wearing silk fabric almost 4700 years ago. Also, you know, guilds of silk weavers prominent to the country’s silk industry are provided in the Arthashastra and the Gupta inscriptions. The Gupta period established India’s status as a major silk exporter through the Indian Ocean trade, where Romans remained the most significant importer of Indian silk, and the Persians monopolized it. Furthermore, Akbar played an active role in overseeing royal textile workshops across his provision.” After listening to this fact, Sudhir’s mouth went open in awe.
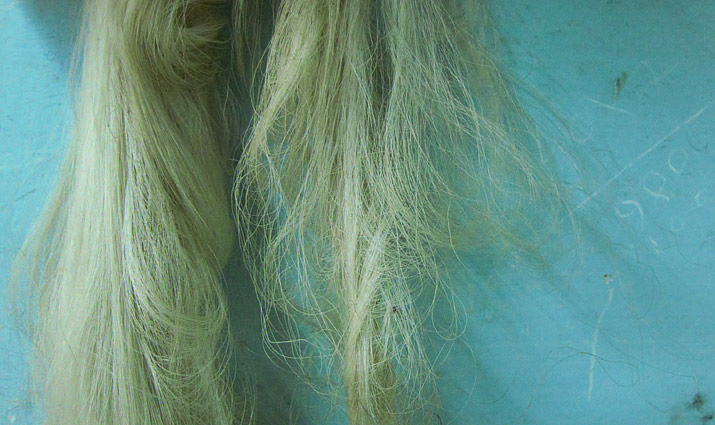
Now, Balkrishna and Sudhir were nearing the final destination of their trip, and the father began explaining the last type of silk. They were on their way to the weavers, which brought in an exciting coincidence: the last silk variety, eri silk, is perhaps the only silk that cannot be reeled but only spun. Produced from the domesticated silkworm, Philosamia Ricini, that feeds almost entirely on castor leaves, eri silk is limited to Assam, Bihar, Manipur, Meghalaya, Nagaland, and West Bengal. With alternate names of endi and errandi, this naturally copperish-colored silk holds an essential status within the tribes of India. The household practice of sericulture to obtain protein-rich pupae, a delicacy for most tribes, is still prevalent in certain parts of the country. Furthermore, tribes in the northeastern states, especially Assam, have the prevailing culture of indigenously preparing chaddars from eri silk.
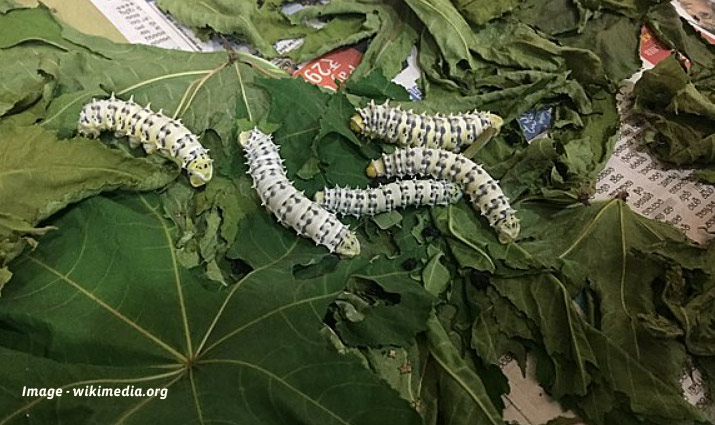
Then, Balkrishna came to a halt in front of the handloom weaving unit, pulling Sudhir out of his reverie of northeast India, back onto the final stage of the process. Although Sudhir had already been exposed to power looms since there is a galore of them around Bangalore, handlooms were hard to find and learn about. The pair walked inside, and Sudhir got instantly fixated on the ceiling where hundreds of threads were dangling, some vertical, some horizontal, almost surrounding the little boy in an enchanting setup. These parts, moving up and down rhythmically, were being controlled solely by the weaver’s feet. Their hands were simultaneously preoccupied as well, sliding other parts side to side. This lengthy process of almost 1-3 weeks finally produces an elegant silk saree.
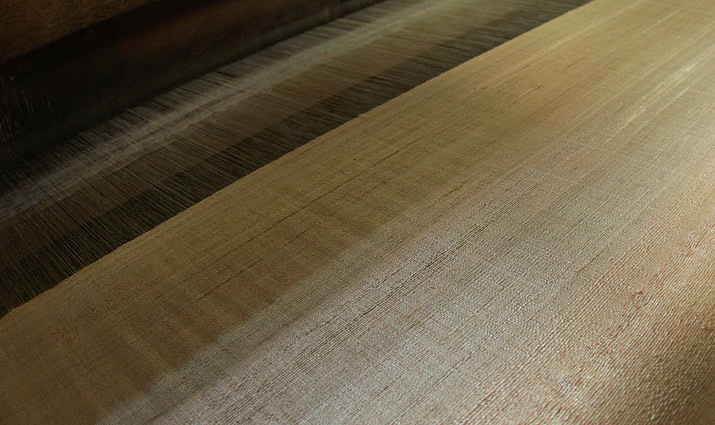
From cocoons to reeling and finally weaving, the silk journey is a long process but a significant part of India’s textile industry that left a lasting impression on Sudhir’s young mind. While heading back home, Sudhir expressed his gratitude towards the silkworm that gives life to cover the body. Seeing such interest in a young boy, Balakrishna went on to explain to his son the work Gandhi did in the field of ahimsa silk, where the moth was allowed to escape their cocoon after which the fibers were spun. Hearing this brought a huge smile to Sudhir’s face, and left him satisfied, as he walked back home.