Tikamgarh Metal
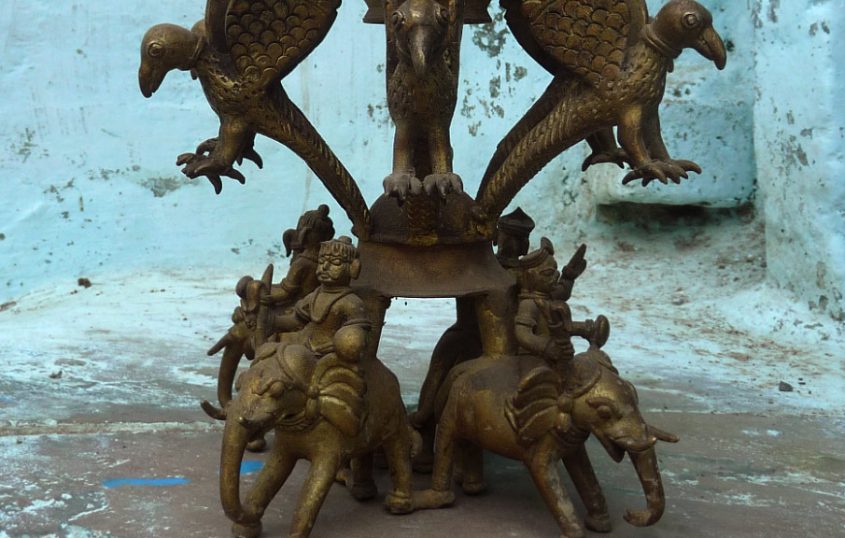
Four hundred kilometers, one in the south and the other in the north of the state of Madhya Pradesh, two very similar, yet distinct crafts… One, practiced by the tribals, for ceremonial and daily use, the other, crafted for kings, for weapons and canons, temple décor and bells. One, whose imperfections give it the naïve charm, and the other, where an error is unacceptable, both, melting metal and wax and creating beautiful objects…
Somewhere near the edge of Uttar Pradesh and Madhya Pradesh, in Tikamgarh, bell metal casting has been practiced for about three to four centuries. From canons and war weapons for kings and soldiers, to bullock carts and cattle bells for the farmer, to even real gold temple decorations, metal smiths here crafted almost every object of need and desire.
The process of casting used in Tikamgarh is similar to the Dhokra casting in Betul, as both the crafts take shape with lost wax casting, a common process used to cast objects in metals. But while the Dhokra of Betul is created with strings of wax on individual pieces, in Tikamgarh, the metal pieces are sculpted in the usual way and moulds are created to replicate the objects.
A mixture of industrial wax, groundnut oil and a binding resin locally known as “rar” is heated and used as the modeling material. In case of larger articles, a clay base is made, over which this wax mixture is coated and given the finer shapes. Craftsmen have devised indigenous tools for their specific needs, spatulas and rolling pins for rough shaping, chisels and knives for finer carving and even small moulds for those tiny, painstaking details.
Once the wax hardens, it is covered with a thin layer of a local red soilsieved with a fine cloth and mixed with water so as to reach every crevice of the wax sculpture. A thick paste of red mud and cow dung coats this, and once it dries, it is covered with “bajari” (sand) and black soil. Two holes, one for the out flow of wax and one for pouring in the metal, are made in these thick covering layers. This entire process of coating the wax model with different kinds of mud mixtures itself takes up to 7 days.
This mud covered wax article object is baked in a furnace powered by coal and cow dung cakes. Wax melts and flows out of one opening, while molten metal, usually brass or bell metal is poured in to fill the space. The baked mud cover is broken when it cools, to reveal the sculpted piece of art. This is finally polished, or given an acid treatment for an “antique” finish.
The number of craftsmen in Tikamgarh, once famous for its bell metal work, has reduced from 70, some sixty years back, to just a handful now. Nevertheless, this craft that once catered to the kings, now caters to a worldwide audience with its exceptional workmanship in brass and copper. Craftsmen make toys, figures of animals and gods, lamps and vesselsto be sold in local as well as export markets. They have even made hugesculptures for government buildings and continue to do remarkable work in this field.
Two similar crafts of the same state, one symbolizing the simple life in the forests of central India and the other, associated with palaces, forts and great temples, yet both born of wax and molten metal, like two brothers growing up into their own calling, their own destinies and wonderful radiant worlds.
Tikamgarh Metal Casting in Detail ~ Gaatha.org